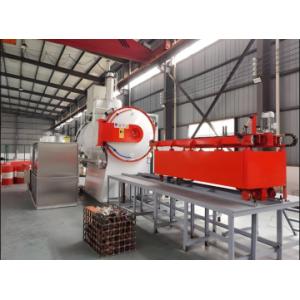
Add to Cart
A vacuum furnace is a critical piece of equipment in many industrial processes, designed to provide superior thermal treatment in a controlled environment. Known for its ability to achieve high vacuum conditions, precise temperature control, and energy efficiency, the vacuum furnace is highly versatile, serving various industries such as aerospace, automotive, metallurgy, and electronics manufacturing.
One of the key advantages of a vacuum furnace is its ability to reach ultra-high vacuum levels. This feature is crucial in processes where oxidation must be avoided, especially in heat treatment of metals, where maintaining material purity is essential. The high vacuum environment allows for the processing of sensitive materials like titanium and superalloys, as well as for the production of components that require tight tolerances and minimal contamination, such as in semiconductor or medical device manufacturing.
By removing the presence of oxygen and other gases, a vacuum furnace ensures that oxidation, scaling, or chemical reactions that could degrade the material’s surface quality are prevented. This makes it ideal for manufacturing products where high precision and surface integrity are necessary, such as turbine blades, aerospace components, and medical implants.
A critical aspect of the vacuum furnace is its precise temperature control. These furnaces are equipped with advanced heating systems and thermal sensors that allow for tight regulation of temperatures, often within a few degrees of the set point. This accuracy is vital for processes like annealing, sintering, and brazing, where even slight temperature variations can affect the mechanical properties of the final product.
The ability to control the heating and cooling cycles also enables vacuum furnaces to process materials with specific thermal requirements. For example, in the heat treatment of steel alloys, maintaining precise temperatures during quenching and tempering directly affects the hardness and strength of the finished product.
Modern vacuum furnaces are designed with energy efficiency in mind, incorporating features that reduce energy consumption while maintaining optimal performance. The use of insulating materials in the furnace’s design minimizes heat loss, and advanced control systems allow for more efficient power usage during heating cycles.
Energy-efficient vacuum furnaces not only help reduce operational costs but also support sustainability initiatives by minimizing the environmental impact of industrial processes. This makes them a preferred choice for manufacturers looking to optimize both performance and cost-effectiveness in their production lines.
The versatility of vacuum furnaces is one of their greatest strengths. They can be used in a wide range of applications, from the simple heat treatment of metals to complex processes like sintering ceramics, degassing, and vacuum brazing. In addition to metals like steel, copper, and aluminum, vacuum furnaces can process exotic materials such as superalloys, carbon composites, and advanced ceramics.
In industries like aerospace, where component reliability and material strength are paramount, vacuum furnaces are used for heat treating turbine blades, engine parts, and structural components. The automotive industry relies on them for the hardening of gears, shafts, and other drivetrain components. The electronics industry benefits from vacuum furnaces for annealing semiconductor wafers and fabricating high-precision circuit boards.
A vacuum furnace works by creating a vacuum inside its chamber, which removes air and other gases. This creates an inert environment where materials can be heated without oxidation or contamination. The heating elements within the furnace bring the material to the desired temperature, and the vacuum helps maintain a controlled atmosphere.
The main components of a vacuum furnace include:
The advantages of using a vacuum furnace include:
Vacuum furnaces can treat a variety of materials, including:
The vacuum level is maintained through the use of vacuum pumps and seals. Common types of vacuum pumps include mechanical, diffusion, and turbomolecular pumps. Seals are typically made from materials like rubber or metal gaskets to ensure a tight seal around the chamber.
Safety precautions include:
Vacuum furnaces provide a perfect combination of high vacuum capability, precise temperature control, energy efficiency, and versatile applications. Their ability to process a wide range of materials with strict temperature and environmental requirements makes them indispensable across various industries. As manufacturing demands grow more complex, vacuum furnaces will continue to play a crucial role in delivering high-quality, reliable components for some of the world’s most critical applications.